2016 Winners
Winners of the 2016 Excellence in Concrete Construction Awards
ACI recognized 13 winners at the 2016 Excellence in Concrete Construction Awards Gala during The ACI Concrete Convention and Exposition, October 24, 2016, in Philadelphia, PA.
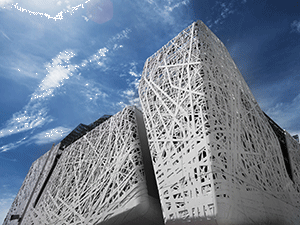
Overall “Excellence” Award Winner/First Place – Category: Decorative Concrete
Palazzo Italia (Italian Pavilion Expo 2015). Milan, Italy. The Italian Pavilion is the throbbing heart of Expo 2015. The architectural design envisages the construction of a complex structure whose exterior and some interior spaces recall the shapes of branches in a thick forest. The entire outdoor surface and part of the interiors consist of i.active BIODYNAMIC cement panels, obtained using Styl- Comp technology from the new material developed at i.lab, the heart of Italcementi’s research and innovation. The “bio” component is given by the product’s photocatalytic properties, originating from the active ingredient TX Active, patented by Italcementi. In direct sunlight, the active principle contained in the material “captures” certain pollutants present in the air and converts them into inert salts, helping to purify the atmosphere from smog. The “dynamic” component is a specific characteristic of the new material, whose particular fluidity allows the creation of complex shapes like those found in the Palazzo Italia panels.
Description of Project and Project Demographics: Project Size: 13,000 m², 2500 tons biodynamic cement, Construction Duration: 10 months
Project Team Members: Owner: Expo 2015 spa; Architect: Nemesi & Partners srl; Engineering Firm: Bms progetti srl and Proger Spa; General Contractor: Italiana Costruzioni; Concrete Contractor: Styl-Comp; Concrete Supplier: Italcementi.
Nominating ACI Chapter: Italy
First Place – Repair and Restoration
The Strand, American Conservatory Theater (A.C.T.) San Francisco, CA. The transformation of an abandoned, century-old movie theater into a highly visible, alternative, experimental performance space for San Francisco’s preeminent theater company is a major milestone in the regeneration of the midsection of Market Street. The new structural system consists of a metal deck roof diaphragm over the original auditorium trusses, ductile reinforced concrete and reinforced masonry shear walls integrated with the spatial expression of the interior spaces, and a mixture of reinforced concrete slabs and beams and steel and composite metal deck floor framing all supported on new, shallow reinforced concrete foundations and grade beams. Useable area was created for actors’ changing rooms and other support functions by excavating to create a reinforced concrete basement structure below the stage between existing foundations. The project team worked closely with historic preservation architects to retain and reuse as many of the original materials and features as possible, including the masonry façade and internal finishes. To restore the façade, decorative glass fiber-reinforced concrete panels were cast from molds made from the existing relief and installed below the building’s canopy to extend the ornamentation to the ground.
Description of Project and Project Demographics: Project Size: 20,000 ft², 1800 tons of concrete, Construction Duration: 12 months
Project Team Members: Owner: American Conservatory Theater; Architect: Skidmore, Owings & Merrill LLP; Engineering Firm: Skidmore, Owings & Merrill LLP; General Contractor: Plant Construction Company LLP; Concrete Contractor: Bradley Concrete; Concrete Supplier: Central Concrete; Development manager, project manager, and financing consultant: Equity Community Builders, LLC; Mechanical design build engineers: Anderson Rowe & Buckley, Inc.; Civil engineering: BKF Engineers; Acoustics, security, and telecommunications: Charles M. Salter Associates Inc.; Electrical design build engineers: Decker Electric Co., Inc.; MEP design engineers: WSP | Parsons Brinckerhoff; Historic preservation consultant: Page & Turnbull, Inc.; Plumbing design-build engineers: Pribuss Engineering, Inc.; Lighting design: PrichardPeck Lighting, Inc.; Theater consultant: The Shalleck Collaborative, Inc.; LEED® consultant: Rick Unvarsky Consulting Services, Inc.; Architectural concrete finishing/polishing: Bay Area Concrete Mold-cast glass fiber reinforced concrete ornamentation: Giampolini Courtney (with Architectural Facades Unlimited).
Nominating ACI Chapter: Northern California and Western Nevada Chapter
Second Place – Repair and Restoration
F.E. Weymouth Water Treatment Plant Filter Buildings Seismic Upgrades. La Verne, CA. Placed into service in 1941, this building is one of Metropolitan’s oldest and one of the most architecturally significant, with striking California Mission and Spanish architectural design features. Almost 75 years after its completion, the facility required a major rehabilitation, including extensive seismic modifications and concrete restoration entailing demolition of structural concrete sections to retrofit columns and beams. Metropolitan and the entire construction team worked painstakingly to bring the building up to current building standards while fully preserving its historic beauty and keeping the facility fully operational.
Description of Project and Project Demographics: Project Size: 48,000 ft², 600 cubic yards of concrete, Construction Duration: 18 months
Project Team Members: Owner: Metropolitan Water District of Southern California; Architect: Metropolitan Water District of Southern California; Engineering Firm:Metropolitan Water District of Southern California; General Contractor and Concrete Contractor: JF Shea; Concrete Supplier: Holliday Companies; Construction Management: Metropolitan Water District of Southern California.
Nominating ACI Chapter: Southern California
First Place – Flatwork
Brisbane West Well Camp Airport (BWWA) EFC Geopolymer Pavements. Wellcamp, Queensland, Australia. Brisbane West Wellcamp Airport (BWWA) is Australia’s first public airport to be built in 48 years. BWWA opened on November 11, 2014, marking a very significant milestone in engineering: the world’s largest modern geopolymer concrete project. Construction of the heavy-duty 435 mm thick aircraft pavements at BWWA was undertaken using a geopolymer concrete that contained absolutely no portland cement. The finished pavements are now in service and provide an excellent example of achieving massive environmental improvement with concrete without compromise on strength, durability, or cost. Achieving an exemplary environmental outcome along with cost competitiveness, durability, and structural performance were key criteria of the project brief. The environmental benefit of EFC is achieved through the replacement of carbon-intensive portland cement with two major recycled wastes from industry—blast furnace slag from steel production and fly ash from coal-fired power generation.
Description of Project and Project Demographics: Project Size: 50,500 m², 45,560 tons of concrete, Construction Duration: 4 months
Project Team Members: Owner: Wellcamp Airport; Engineering Firm: ACG; General Contractor: Wagners Civil; Concrete Contractor: SEC; Concrete Supplier: Wagners Concrete.
Nominated by: Concrete Institute of Australia
Second Place – Decorative Concrete
Stealth. Atlanta, GA. Stealth is a contemporary urban sculpture. The monolithic cast-in-place reinforced concrete form stands 33 ft tall in the plaza of the Promenade Tower in the Arts District of Midtown Atlanta. The piece is a spatial work of cognition, illusion, and transformation. The sculpture acts as an urban instrument, binding neighboring spaces through visual corridors. The sculpture was analyzed with SAP finite element program, using a generated mesh and varying thicknesses of elements to simulate the elliptical cross section of the sculpture. The upper portion is 7 in. thick and is dominated by shell behavior with relatively low stresses and is reinforced with a two-way mat of No. 5 reinforcing bars at 4 in. on center. The lower portion is 14 in. thick and is dominated by bending behavior with high stresses resisted by two No. 7 reinforcing bars at 4 in. on center vertically with No. 5 horizontal ties at 4 in. on center. The structure is founded on a 16 in. thick mat foundation to support its 65,000 lb weight and resist overturning wind loads.
Description of Project and Project Demographics: Project Size: 65,000 lb and 33 ft tall, 65 cubic yards of concrete, Construction Duration: 12 months
Project Team Members: Owner: Cousins Properties; Architect: Formations Studio; Engineering Firm: Uzan+Case, LLC; General Contractor and Concrete Contractor: Sinclair Construction Group; Concrete Supplier: Thomas Concrete of Georgia; Concrete Shaping and Polishing: NOVA Commercial Interiors
Nominating ACI Chapter: Georgia
First Place – Category: Low Rise Buildings
Museo Internacional del Barroco. Puebla, Mexico. Three main concepts have been addressed while designing the museum: one—from a rigid order, space melts and creates fluid spaces; two: beautiful light; and three: an ecological mechanism and the care of the environment. Conceptually, it is imagined that the building flows out from the land as a spring and grows. The structure was based on a system of apparent white concrete prefabricated walls and smooth finish acid, with the purpose to finish quickly, deleting the process of casting and curing concrete, and reduce labor with little investment in equipment. A challenge was to get the aesthetic finish—which was intended to be perfect, unblemished, and homogeneous in appearance—for which steel formwork were used with an exhaustive control of joints between pieces.
Description of Project and Project Demographics: Project Size: 18,149 m², White Concrete Volume = 2650 m³; Gray Concrete Volume = 20,860 m³ of concrete, Construction Duration: 10 months
Project Team Members: Owner: Grupo Hermes Infraestructura; Architect: Toyo Ito & Associates, architects; Engineering Firm: SC3, S.C; General Contractor: Secretaria de Educación Pública; Concrete Contractor: Danstek; Concrete Supplier: CEMEX.
Nominating ACI International Partner: IMCYC
Second Place – Category: Low Rise Buildings
Frost Museum of Science. Miami, FL. The new Patricia and Phillip Frost Museum of Science will support innovation and creativity inherent in Miami’s richly diverse community. With its real-life marvels, interactive exhibits, and exciting learning adventures in a state-of-the-art, energy efficient building, Frost Science will introduce basic concepts of science and technology. The concrete begins with a below-grade parking garage level containing defined formwork seam patterns on exposed concrete surfaces. The first floor is the Plaza level, connecting all of the buildings and exhibits of the Science Museum. There are two tower structures to house exhibit galleries and museum offices, connected by an openair exposed concrete breezeway and flanked by the domed Planetarium structure. Connecting bridges also span to the Living Core Structure, a four-story building that houses seven architectural concrete aquarium exhibits and a goliath concrete roof structure. Every yard of concrete contained at least 50% slag cementitious replacement, improving sustainability for LEED accreditation. The Planetarium is a one-of-a-kind spherical concrete structure, with the lower half being architectural cast in place concrete. The dome extends over three stories from the ground and 85 ft in diameter, with the top half of the sphere being precast.
Description of Project and Project Demographics: Project Size: 250,000 ft², 30,000 yd³ of concrete, Construction Duration: 2.4 years
Project Team Members: Owner: Patricia and Phillip Frost Museum of Science; Architect: Rodriguez and Quiroga Architects Chartered; Engineering Firm: D.D.A. Engineers; General Contractor: Skanska USA Building; Concrete Contractor: Baker Concrete Construction; Concrete Supplier: Supermix Concrete, Inc.; Design Architect: Grimshaw Architects.
Nominating ACI Chapter: South Florida
First Place – Category: High Rise Buildings
Children’s Hospital of Richmond at VCU. Richmond, VA. Children’s Hospital of Richmond at VCU is a multi-story, 640,000 ft², high-tech outpatient pavilion for pediatric services. The Children’s Pavilion will be the largest, most advanced outpatient facility dedicated to children in the region, including diagnostic and treatment services for children. 11,000 yd³ of 5000 and 7000 psi concrete was placed in a mass foundation. Mass specification requirements had traditional high-temperature (160°F) and differential temperature (35°F) requirements. The mixtures needed to be pumped and have an SCC consistency to move through 6 to 7 ft of a highly reinforced mat with limited external consolidation. Cast-in-place was used in 4600 yd³ of 3500 psi pumped structural lightweight concrete; 15,000 yd³ of low-permeability (1000 coulomb) 5000 psi pumped structural, fiber-reinforced concrete for the parking garage; and 6650 yd³ of 7000 and 8000 psi high performance for columns and shear walls. The completed structure has been designed for future horizontal and vertical expansion.
Description of Project and Project Demographics: Project Size: 640,000 ft² multi-story, 40,395 yd of concrete, Construction Duration: 2 years
Project Team Members: Owner: VCU Health; Architect:HKS Architects; Engineering Firm: Dunbar Milby Williams Pittman & Vaughan; General Contractor: Skanska USA Building, Inc.; Concrete Contractor: Cleveland Cement Contractors; Concrete Supplier:Vulcan Materials Company.
Nominating ACI Chapter: Virginia
Second Place – Category: High Rise Buildings
McCord Hall at ASU W.P. Carey School of Business. Tempe, AZ. The W.P. Carey School of Business added a new state-of-the-art building to their current facilities on Arizona State University’s Tempe campus. McCord Hall is the new home for the graduate, MBA, and Executive Education programs. A monumental four-story concrete arcade frames the entrance to the school from both sides of the campus at the northeast corner, while to the southwest, the plaza opens up to welcome visitors and the business school community. McCord Hall is designed to be a reusable structure that can be re-purposed without having to be demolished for up to 100 years and possibly longer. Each building has a unique post-tensioned solution that consisted of a two-way flat plate design for the north building and a one-way slab with shallow dropped beams at each radial grid on the south building. The buildings were linked at each floor with a long-span open skyway constructed with radiused cast-in-place concrete T-beams supported on haunches at the expansion joint. The lateral system consisted of intermediate concrete shear walls which were designed using the simplified analytical method and redesigned using dynamic analysis procedures, which resulted in the removal of one wall from the first floor to the roof and reduced the overall cost of the lateral system by 15%.
Description of Project and Project Demographics: Project Size: 129,000 ft², 8040 yd³ of concrete, Construction Duration: 20 months
Project Team Members: Owner: Arizona State University; Architect: RSP Architects; Engineering Firm: Meyer Borgman Johnson; General Contractor:DPR Construction; Concrete Contractor: Suntec Concrete.; Concrete Supplier:Hanson.
Nominating ACI Chapter: Arizona
Second Place – Category: High Rise Buildings
Viktoria. Seattle, WA. The Mission Bridge is a major four-lane, 1-km long crossing of the Fraser River in British Columbia, Canada. It was opened to traffic in 1973. The bridge is located in a high seismic zone and is a critical lifeline link in the Province’s disaster recovery network. The crossing is one of the nine major crossings prioritized for seismic retrofit, spurred in large part by the 1989 Loma Prieta earthquake in San Francisco. This project exploited the unique properties of UHPC to solve a significant challenge in the seismic retrofit of large concrete columns. A novel UHPC column jacket as a seismic retrofit was a critical last step in this retrofit project.
Description of Project and Project Demographics: Project Size: 300,000 ft², 14,500 yd³ of concrete, Construction Duration: 15 months
Project Team Members: Architect:Weber Thompson; Engineering Firm:Cary Kopczynski & Company (CKC); General Contractor:Turner Construction; Concrete Contractor: Turner Construction; Concrete Supplier:Cal Portland; Developers: Goodman Real Estate and Mack Urban.
Nominating ACI Chapter: Washington
First Place – Category: Infrastructure
The "Ring of Memory" International Memorial of Notre-Dame-de-Lorette. Ablain-Saint-Nazaire, Paris, France. The "Ring of Memory" International Memorial has been built to celebrate the first World War Centennial at the very place of one of its most murderous battlefields near Arras (Northern France), close to the largest French War Cemetery on the crest dedicated to Notre-Dame de Lorette. The International Memorial is an outstanding architectural achievement, but it is also a technical challenge. The Ring is composed of two distinct structures. The first one consists of standard precast segments with thin walls (4 cm thick), resting directly on the ground. The second is a three-span curved bridge, 125 m in length with a main span of 56 m, realized using precast segments assembled by post-tensioning. Indeed, its very particular geometry is associated with very high flexural-torsional stresses. Only ultra-high-performance fiber-reinforced concrete, namely the BSI® (Béton Spécial Industriel) developed by Eiffage Group, made it possible to meet the special structural, durability, and architectural requirements to create this impressive fence favoring meditation.
Description of Project and Project Demographics: Project Size: Perimeter of the ellipse: 328 m Floor area: 1155 m², 300 m³ of concrete, Construction Duration: 1 year
Project Team Members: Owner:Région Nord Pas-de-Calais; Architect:AAPP Agence d'Architecture Philippe Prost; Engineering Firm:C&E Ingénierie; General Contractor:Eiffage TP Nord - Eiffage VIA PONTIS - Eiffage Energie; Concrete Contractor: Atelier Artistique du Béton; Concrete Supplier:Eiffage VIA PONTIS.
Nominating ACI Chapter: Paris
Second Place – Category: Infrastructure
3rd Bosphorus Project. Istanbul, Turkey. Eight lanes of motorway and two lanes of railway will be located at the same level on the 3rd Bosphorus Bridge. A bridge of firsts, the 3rd Bosphorus Bridge is going to be the widest suspension bridge in the world with a width of 59 m and the longest spanning bridge that has a rail system on it, with a main span of 1408 m. Another first for the bridge is that it is the suspension bridge with the highest tower in the world, with a height of more than 322 m. The tower structures are built with reinforced concrete up to a height of 305 m, and the rest is a steel saddle for main cables. The compressive strength of the concrete used in the project is classified as C50/60 and it fulfils various durability requirements because it needs to provide at least 100 years of service life under rough environmental conditions. Including foundations, 104,000 m³ of concrete was used for the construction of the four pylons of the bridge.
Description of Project and Project Demographics: Project Size: 1422 m, 2,435,715 m³ of concrete, Construction Duration: 3 years
Project Team Members: Owner: ICA (IC Ictas-Astaldi JV); Architect and Engineering Firm: Jointly by structural engineer Michel Virlogeux, and T-Engineering; General Contractor: IC ÇTA; Concrete Contractor and Concrete Supplier: Akçansa Çimento Sanayi ve Ticaret. A.
Nominating ACI Chapter: Turkey